- Corporate
- News
- Custom Design Services
- Products
- FAQ
- Contact Us
-
Products Of The Month
Custom Design Services
Bottle Painting
Erbatur adds a unique touch to perfume bottles with matte coating and special coloring techniques. Gradual painting, which enriches the content by emphasizing certain areas or color transitions, offers a unique aesthetic to each bottle. Erbatur's art of bottle painting reflects the quality of the brand with its colorful and original designs.
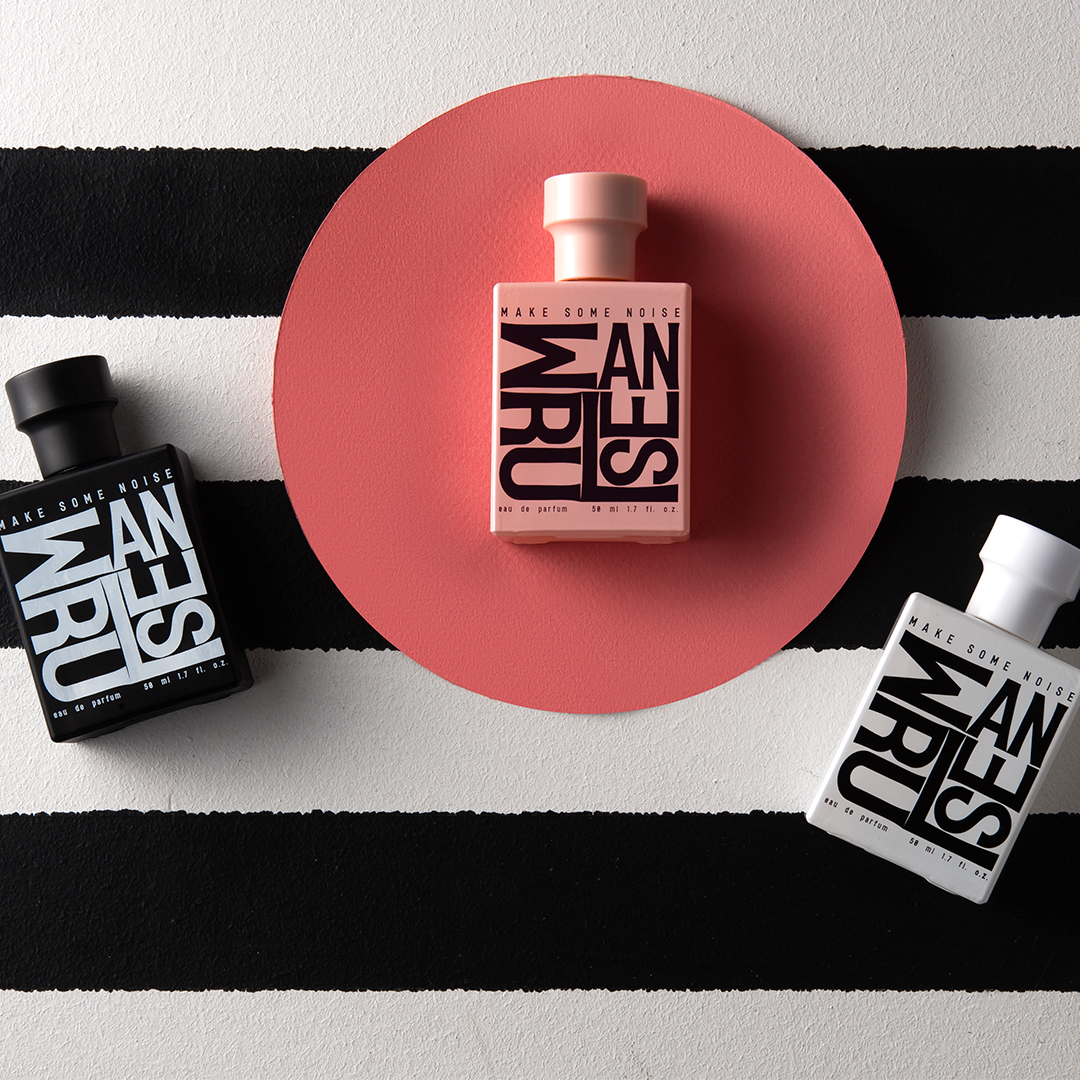
Matte Coating
Matte coating is a paint process that reduces the gloss of the surface, giving it a matte appearance. Perfume bottle dyeing, on the other hand, is a process performed to achieve a more aesthetic appearance by providing a color change.
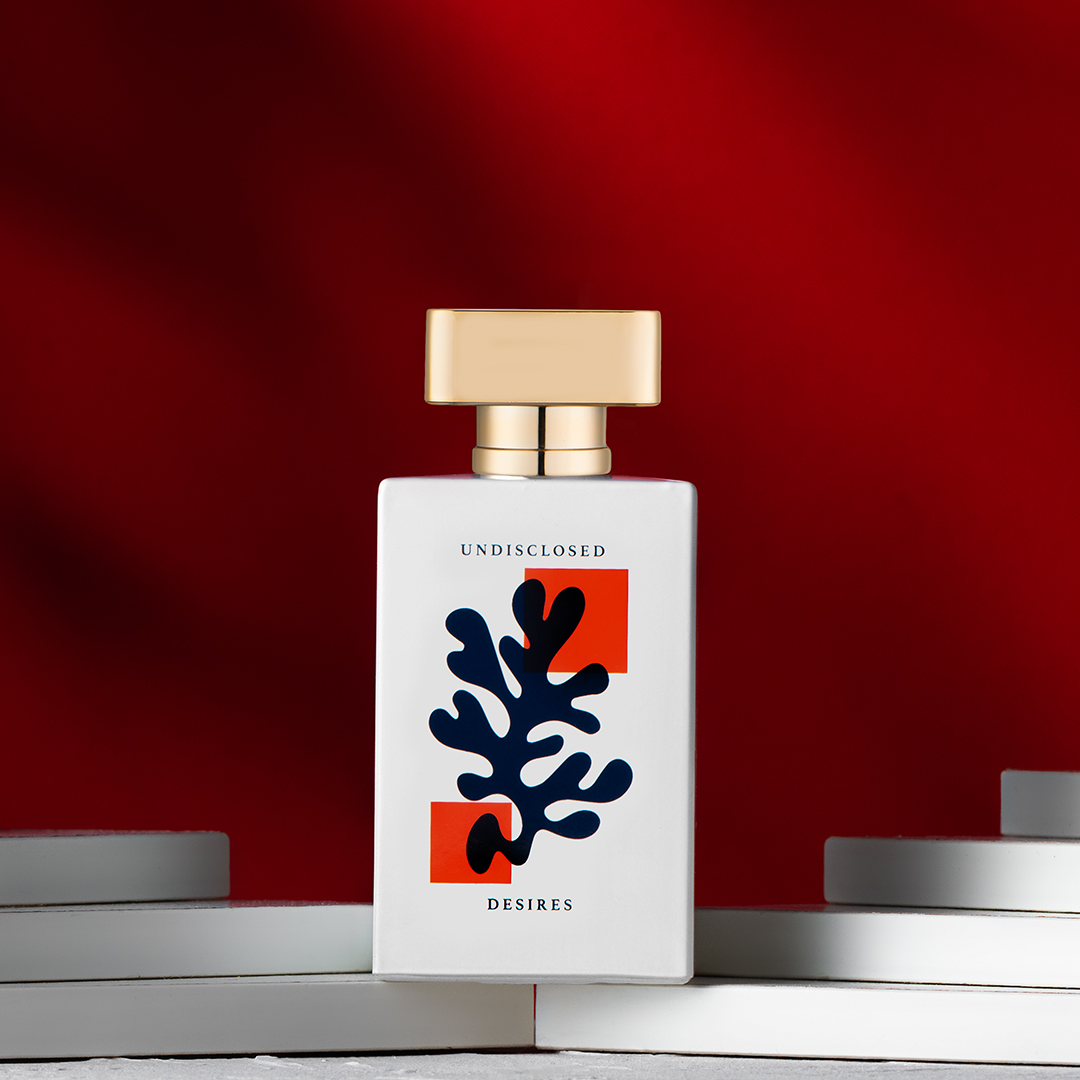
Gradual Coating
Partial perfume bottle dyeing is the process of dyeing only a certain area of a perfume bottle. This process is generally used to make only a certain part of the bottle stand out or to make the design more attractive.
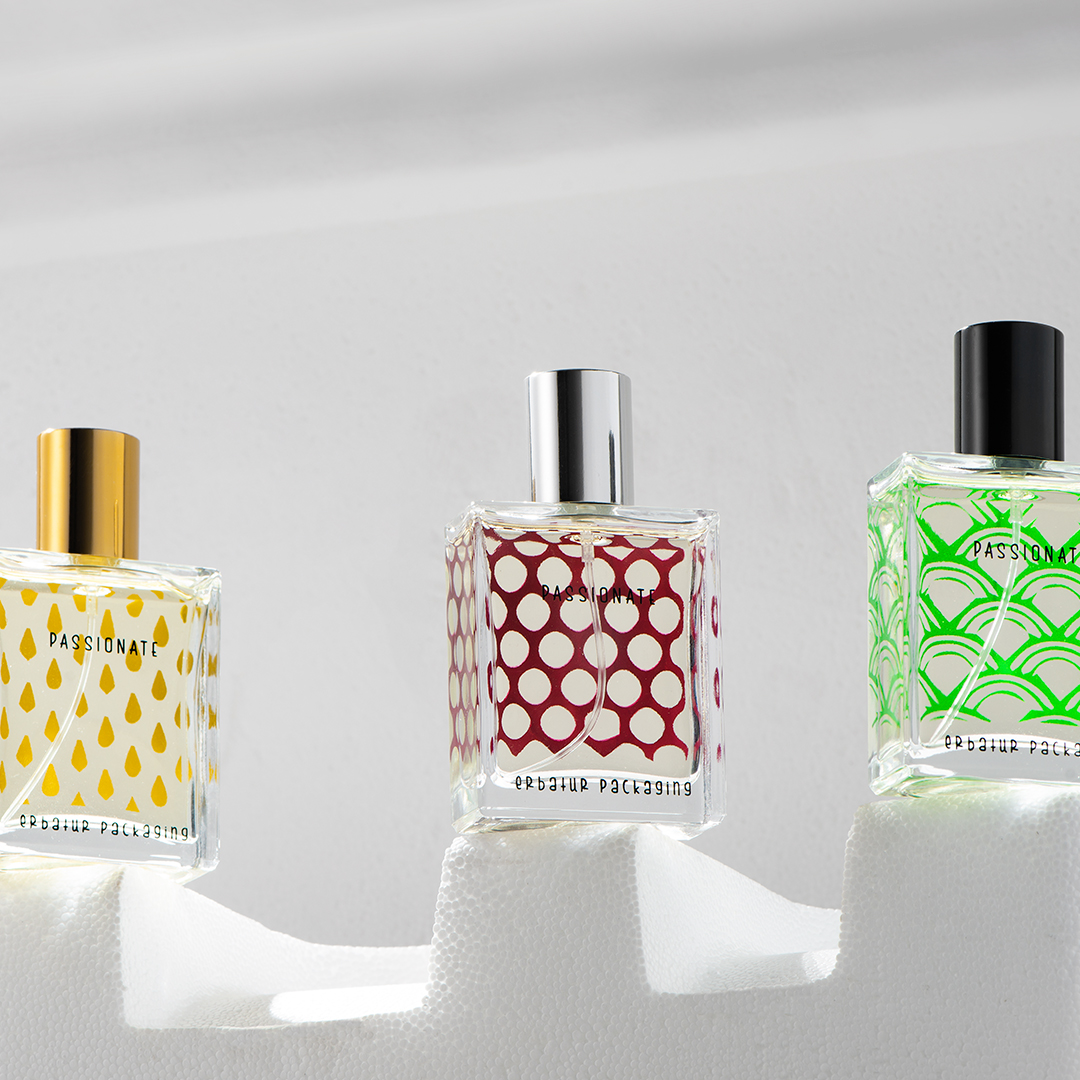
User Partial Coating
Gradual perfume bottle dyeing is the process of applying more than one color to a perfume bottle, creating a color transition or gradient inside the bottle. This technique is different from the traditional painting process applied to the surfaces outside the bottle. türkçesi
Perfume Bottle Painting
Perfume bottle painting is a specialized craft that enhances the aesthetic appeal of the bottles, making them not just containers for fragrances but also decorative objects. This process involves various techniques and materials, each contributing to the final appearance and feel of the product.
Perfume bottle painting is a blend of art and technology, requiring precise techniques and high-quality materials to produce visually appealing results. This craft not only enhances the visual appeal of perfume bottles but also contributes significantly to brand identity and customer attraction. Whether employing manual skills for bespoke designs or automated methods for mass production, the choice of technique and materials plays a crucial role in achieving the desired outcome.
Perfume Matte Coating About
The matte finish is a popular choice for perfume bottles, increasing the aesthetic value of the product while also providing practical advantages. The matte coating process is achieved by a coating or process applied to the surface of the bottle and uses thermoplastic materials. This process gives the outer surface of the bottle a smooth and opaque appearance.
Features and Advantages of Matte Coating:
Aesthetic Appearance: Matte finish offers a modern and sophisticated appearance. It can distinguish your product from its competitors by providing a simpler aesthetic compared to glossy surfaces.
Tactile Feel: Matte surfaces offer users a smooth and satin touch. This feature makes the product feel higher quality when held in hand.
Fingerprint Resistance: Matte coatings show fingerprints and smudges less than glossy surfaces. This helps the product look consistently clean and attractive.
Color Options: Matte coating can be applied in a variety of color options, so it can be customized to match your brand's color scheme.
Durability: The matte finish also makes the surface more resistant to scratches and wear, which contributes to the longevity of the product.
Application Process:
The matte coating process is usually carried out during the production stage of the bottle. The coating material is applied by spraying the bottle surface or by dipping it in a coating container. The coating is fixed to the surface using adhesives or binders. This process ensures that the coating spreads evenly over the surface and provides long-term durability.
When applied to perfume bottles, the matte finish offers an elegant and distinctive appearance that makes the product stand out in the market. In addition to leaving a quality impression among consumers, matte surfaces help the brand portray a modern and innovative image.
Perfume Gradual Coating About
Perfume bottles with a gradual coating, also known as gradient or ombre coating, represent a sophisticated aesthetic that elevates the visual appeal and branding of the product. This type of finish involves a seamless transition between colors, creating an elegant and eye-catching effect that can significantly enhance the consumer's perception of the perfume. Here’s an in-depth look at the process, techniques, and considerations involved in creating a gradual coating on perfume bottles:
Techniques for Creating Gradual Coating
-
Spray Coating: This is the most common method used for achieving a gradient effect. The process involves using an airbrush or spray gun to apply the paint or coating. By adjusting the spray pressure, the angle of application, and the mix of colors, artisans can create a smooth transition between colors. This method requires skill to ensure that the gradient is even and blends naturally.
-
Dip Dyeing: Another technique is dip dyeing, where the bottom or top of the bottle is dipped into a dye solution, and the color intensity decreases as it moves up or down the bottle. The depth and duration of the dip affect the gradient’s appearance, making this method less precise but uniquely variable in its results.
-
Manual Blending: For smaller batches or bespoke designs, manual blending of paints on the bottle surface can be employed. This involves hand-painting the colors and then blending them while still wet to achieve the desired gradient effect.
Materials Used
-
Lacquers and Enamels: These materials are commonly used for their durability and vibrant colors. They adhere well to glass and can withstand the wear and tear of handling and use.
-
UV-Curable Inks and Coatings: Ideal for fast processing, UV-curable materials harden under UV light, providing a quick and durable finish. They are particularly useful for high-volume production lines.
-
Solvent-Based Coatings: These coatings are used for their ability to create smooth, even layers, but they require proper handling and ventilation due to the volatile organic compounds (VOCs) they emit.
Surface Preparation
Proper surface preparation is critical to achieving a high-quality finish. This usually involves cleaning the glass to remove any impurities or residues and applying a primer to ensure good adhesion of the coating. Surface activation techniques such as flame treatment or plasma treatment may also be used to increase the surface energy of the glass, improving the coating’s durability.
Curing and Finishing
After application, the coatings need to be cured, which may involve heat treatment or UV curing depending on the type of coating used. The curing process solidifies the coating, enhancing its durability and resistance to environmental factors.
Quality Control and Testing
Quality control is crucial to ensure that each bottle meets the desired aesthetic and performance standards. This includes checking for uniformity of the gradient, color accuracy, and adhesion quality. Durability tests might also be conducted, including scratch resistance and tolerance to temperature changes and sunlight.
Environmental Considerations
As environmental regulations become stricter and consumer preferences shift towards sustainable products, more companies are exploring eco-friendly options for gradual coatings. This includes water-based coatings and those with reduced or no VOCs, which help minimize the environmental impact while maintaining product quality and durability.
Conclusion
Gradual coating on perfume bottles is not just about aesthetic enhancement but also about creating a distinctive identity for a brand. This technique requires precise execution and high-quality materials to ensure that the final product stands out in the competitive perfume market. With advancements in materials and application technologies, the possibilities for creative and appealing designs in perfume bottle coatings continue to expand.
User Partial Coating About
The gradual dyeing technique is used to add aesthetic value to perfume bottles and increase consumer appeal. This method allows us to stand out in market competition by increasing product diversity. Gradual dyeing is a sophisticated surface treatment technique used in perfume bottle production. This method, in which colors slowly blend into each other, significantly increases the visual appeal of the products, maximizing our brand recognition and consumer satisfaction.
Technical Specifications and Application:
Spraying Technique: In this method, paints are sprayed onto the surface of the bottle with air pressure using specially designed spray guns. The color intensity and transition process are controlled by the spray gun settings. The spray distance and angle are carefully adjusted to achieve the desired color transition.
Dipping Technique: Bottles are gradually immersed in the paint. In this process, the speed of immersion of the bottle and the viscosity of the paint affect the smoothness and intensity of color transitions. The immersion depth determines the start and end points of the gradual color effect.
Materials:
Dyes used for gradual dyeing are selected to meet high quality standards. These paints have high resistance to UV rays and environmental factors, which allows the paint to maintain its long-term brightness and vitality.
Paint Types:
Solvent Based Paints: Preferred for their quick drying feature and high pigmentation.
Water Based Paints: They are an environmentally friendly alternative and offer advantages in terms of occupational health and safety.
Quality Control Processes:
Every dyeing process goes through strict quality control processes at every stage of production. Bottles are subjected to detailed inspection before and after painting:
Surface Preparation: Each bottle is cleaned of dust and oil before starting the painting process.
Color Compatibility: After the paint application, the accuracy and transition quality of the colors are evaluated in terms of compliance with the determined standards.
Final Checks: Products are final checked for physical defects such as scratches and cracks.
Cokie Policy
We use cookies on our website to provide you with a better service. By using our site, you are agreeing to accept our Data Policy.
Leave an Email and We Will Contact You
Send email to get in touch
Address
Giyim Sanatkarları Sitesi 2. ada C blok No 319, Kat:3, 34490 İkitelli Osb / Başakşehir / İstanbul
Erbatur Glass © Copyright 2024 | All rights reserved.